Consider the Garment Worker Behind the Price Tag: An Interview With BCWS’ Kalpona Akter
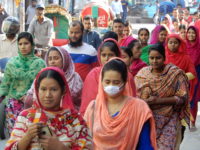
Increasingly, over the last decade, the labels on the cheap clothes at Australian fashion outlets read, “Made in Bangladesh”. And despite rising prices and inflation, the clothing coming out of the South Asian garment manufacturing powerhouse only seems to get cheaper.
When you factor in the profit the company you’re buying from has to be making on a $6 shirt, plus export and transport fees, and the takings of the manufacturer, it’s hard to grasp just how much of the final cost goes directly to the garment maker themselves. And the truth it’s bugger all.
So, for a global consumer standing beneath the neon lighting of their local shopping mall, it’s often easier to push the thoughts of the actual person to the back of their mind, and instead focus on the ridiculously cheap price, and get on with the rest of their day.
Paying with their lives
Over 80 percent of Bangladesh’s exports are readymade garments. And the capital Dhaka is well-known for its legions of garment workers, as well as being notorious for the exploitative and dangerous conditions they often have to work under.
The 2013 Rana Plaza collapse brought the true human cost of the global market’s unquenchable desire for fast fashion. The structurally unsound building housed numerous clothes factories that employed around 5,000 workers, over 20 percent of whom perished in the disaster.
Less than a month after the devastation, global brands, retailers and workers’ unions joined together to produce the Accord on Fire and Building Safety in Bangladesh. And this agreement has proven effective. Today, locals don’t have to work in conditions where they’re literally risking their lives.
And the Accord has not only served to protect garment workers, it’s also made them increasingly aware of their rights. However, the clothing they produce continues to be sold at rock bottom prices over here, which can only mean that while safety has improved, wages remain next to nothing.
A job with dignity
In the 1990s, 12-year-old Kalpona Akter began working in a Dhaka factory. She earned $6 a month working for companies like Walmart. By the time she was 18, Akter had been banned from working in the industry, because she’d tried to start a union in a factory where she’d been employed.
Together with two other former garment workers, Ms Akter went onto form the Bangladesh Centre for Workers Solidarity (BCWS) in 2000. And these days, the workers’ rights organisation has 93,000 solidarity members.
BCWS was instrumental in campaigning for a 70 percent increase in the minimum wage for the local garment sector, it played a role in the establishment of the Accord, and it successfully pushed for international brands to pay compensation to the victims of the Rana Plaza tragedy.
Sydney Criminal Lawyers spoke to BCWS executive director Kalpona Akter about what garment workers actually get paid, the prevalence of gender-based violence in the industry, and how consumers should speak out about the injustices occurring at the other side of the supply chain.
The BCWS is a grassroots workers’ rights organisation representing garment workers both in the formal and informal sectors.
In Australia, there are currently major stores where people can go and buy what seems to be increasingly cheap clothing, which also tends to be produced in Bangladesh.
Ms Akter, when an Australian is about to buy cheap clothing that’s produced in your country. What sort of things should they keep in mind?
If you’re talking about a $3 shirt that consumers in Australia are buying, then they need to assume that the workers at the bottom of the chain are not even receiving 10 cents of that.
So, if you are getting cheap clothes, workers are starving down the chain. This is one thing to think about.
The second is long working hours, because from the designing room to a high street the lead time is really short. It’s a few weeks. So, this is putting workers on long shifts.
And in buying cheap clothes you are ultimately harming the climate, because the research says that to produce one shirt you use 14 litres of water. So, to produce one pair of jeans you are using hundreds of litres.
In buying cheap clothes a consumer is putting a worker in long shift hours, and it’s harming our Mother Earth because it’s hitting our ecological system.
And on top of that, what the consumer is also doing is not using the clothes sustainably. They’re wearing the clothes maybe one or two times and then dumping them.
But, where are they dumping them? Either into the earth, or sending it to a poor country, like Bangladesh, thinking that the people here don’t have any clothes, so let’s give them our second-hand ones. So, they’re using our country again, as a dumping ground.
These are the conditions the workers are facing. And how it’s harming the earth and climate. So, buying cheap clothes is not good. Fast fashion is not good.
Cheap clothes are not cheap. Someone always has to pay for them. And that someone is a worker. And consumers should know this and say no to cheap clothes and fast fashion. They should buy sustainable clothes.
And they should make sure that from the amount they pay, one portion really goes to the worker, regardless of where they’re producing it.
It doesn’t have to be Bangladesh. It can be Vietnam, China or India, because workers are pretty much facing the same problems everywhere.
We’ve got Kmart in Australia, which is like Walmart in the US. If I go to Kmart, I can pick up a shirt from Bangladesh for $6.
However, years ago, it wasn’t possible to buy a shirt for such a cheap price, and there’s been inflation since. So, it seems almost inconceivable how cheap these clothes have become.
It’s crazy. Think about your grandparents. In the winter, how many coats could they have had? Probably one, maybe two. That was sustainable. It paid enough for the person who made it. And they used it for many years.
But, now, the students, have seven coats for seven days. And then next week, they think they have to change them. It’s because it has become so cheap. It’s because you can buy it for ten bucks.
However, people don’t think about who enjoys the biggest piece of the pie. It’s these brands, like Kmart and Walmart. Those companies don’t even pay the cashiers working in their stores well.
So, the government in Australia should take some steps towards Kmart. The media and the consumers should speak up. The buying power is with the consumers. And if they speak out, the brand has to listen.
We do a lot of speaking tours for consumers. Once we had a speaking tour in the United States. It was right after Rana Plaza. I had a survivor with me. She was just 18 years old. She had been stuck in the rubble of the building for two and a half days. But, luckily, she wasn’t killed.
One day we were protesting outside a Gap store in New York City in the high street, and suddenly it was pouring rain. We needed shelter and we ended up going into the Gap store.
For the factory worker, she’d never actually seen where the clothes were selling before. It was a culture shock for her. She had to ask if she could walk around the store.
And as she was walking around the store, she ended up going up to a shelf of skinny jeans. She was holding them up, looking at them, and I knew exactly what she was going to ask.
She said, “How much do they cost.” And I said, “They’re 75.” But, I didn’t tell her in which currency, because I knew how she would feel. But, then about 20 seconds later, she said, “In which?.” And I told her it was in US dollars.
And the scream she did, because one dollar was 80 takas. She said, “This is one month worth of my salary. And with my fellow workers I produce 1,200 of them per day.” So, where the hell does the money go?”
The majority of the workers have no idea how much what they produce is selling for or how much it costs. If you tell any worker here, they would be really shocked to learn how much you are buying a shirt for.
Even if it’s just $6 in Australia, they’re producing 2,000 pieces a day with less than 60 workers. So, the amount they get out of that shirt is just a few pennies.
This is the reality. So, we need an ethical business model from the brands with whoever the sourcing country is. But, to make that we need a consumer voice, otherwise there isn’t going to be a real change.
If the Bangladesh Centre for Workers Solidarity wasn’t around, where else could these workers turn?
There are many organisations like us these days. But, if there weren’t, then they would have nowhere to go. They would be deprived of their rights, because there’s a strong collusion between the manufacturers and the government.
Many times, our legislators are also our factory owners. In our parliament, over 30 percent are manufacturers, and over 90 percent of them are involved in business. So, it’s a business club. It’s not a parliament.
So, the worker would be in a miserable situation if there was no organisation like ours.
What about gender-based issues being faced by garment workers or issues specifically faced by women?
It’s enormous in the sector. But, it’s not recognised or spoken about, because culturally we have been taught not to talk about any violence. It’s taboo to talk about it.
We are living in a culture where if a woman is raped, the blame goes to them. It’s like, why did that man come to you? It’s your fault, woman. You shouldn’t talk about it. So, basically, the women do not talk.
But, if we talk about gender-based violence, a few years ago, a number of organisations did a survey, and we found that 80 percent of workers are facing sexual harassment in the factory. Eight three percent of workers face gender-based violence either in the factory, commute or community.
It’s a huge number. That’s why we’re working on it. We’re asking for our government to ratify the ILO Convention 190, so as to end or combat gender-based violence and harassment in the workplace.
And are there other issues that women are specifically facing in the factories?
There are many women’s issues in the factory. Menstrual issues. On those days the workers don’t get any sanitary napkins from the factory. They don’t get extra time for drinking water, which is needed. They need to hit the same production quota as other days.
Also, there are day care centre issues. The law says there should be a day care centre on the factory premises or the outside, but that doesn’t happen.
So, that’s why women’s numbers are declining in the industry. It used to be 85 percent, but now it has declined to about 70 percent, according to research last year.
One kind of discrimination that doesn’t occur that much in the industry is wage discrimination. Men and women get pretty much the same wage for the same work.
But, there’s huge discrimination in terms of promotions. The women don’t get promoted, while men do.
In April 2013, the Rana Plaza tragedy happened in an area of Dhaka. It involved the collapse of an eight storey building that contained numerous garment factories. Over 1,100 people died in the tragedy.
This was an extreme event, but how representative would you say it was, or is, of the industry? And has the tragedy led to improvements in the factories?
In terms of safety, yes. But, this is not done by the manufacturers or the government.
With Rana, I don’t believe it’s a tragedy. It was a man-made disaster, which could have been prevented if they had followed the law. They had been doing fake auditing in those factories, saying that they were safe for workers.
Everybody is responsible. The producers and the government. The only ones not responsible are the workers. They were forced to work in the factory, even when they saw the crack in the building, and said they would not go. They were pressured and told that they wouldn’t receive their salaries if they didn’t go.
Before Rana, we were trying to get an agreement signed between the branded retailers and the union to make the factory safer. We were asking for a legally binding agreement. But, the branded retailers did not sign it until the disaster, which killed 1,138 workers.
The agreement we are talking about is the Accord on Fire and Building Safety in Bangladesh. It has been signed by 220 brands and retailers around the globe. Nine Australian brands signed. One did not, which is Just Jeans.
The agreement was between the global business and local unions. And it says it will make the buildings’ structure and electrical systems safe.
The Accord has made a phenomenal change in the last six years. Not with all of the factories, but with 1,600, which have 2.2 million workers. Those factories are safe.
So, in a situation like Rana, would you say that workers were turning up to the workplace with an awareness that the building was structurally unsound, and it could come down?
The workers, yes. They were definitely worried about it. The Accord not only made the factory safer, it also strengthened their voice. So, if they see a crack in the building, now they can literally say no to unsafe work. That wasn’t the case before Rana.
Today, workers can walk outside of a building and say they won’t work in it. They don’t have that fear that they had in the past.
But, one problem that we are going to face is the Accord will run out in mid-2020. And it will be handed over the Readymade Sustainability Council (RSC), which will be run by the manufacturers, the brands and the unions.
But, manufacturers are so powerful over here. And when the brands and manufacturers come together, they always work together.
So, I don’t think they will be running it in the same way that the Accord is running. This will mean that we can assume that we will not be having this safe or as fearless a time without the Accord in the future.
The Bangladesh Centre for Workers Solidarity was formed by three former garment workers in 2000. You’re one of them. How would you describe the work that BCWS carries out on the ground?
A lot of improvements have happened since we started. Long shift hours don’t exist like they did 20 years ago, or in my time, when I was in the factory. But, there are a few things that haven’t improved.
One of them is wages. On the surface they have improved. But, if they’re compared with the cost of living and inflation, I would say they’re even poorer wages than I used to get 20 years ago.
Just think of a worker who is getting $95 a month. She or he is giving 30 or 35 percent of their wages to housing. And it’s not dream housing. It is a 10 by 10 concrete room without a window, and no private bathroom.
Another area is the right to organise and bargain. It’s still difficult. There are a good number of unions that have been registered. But, this is quantity, not quality. And that has been done after Rana Plaza, due to international pressure.
If we talk in terms of whether these workers have a collective bargain agreement, there are less than 50 factories that are functioning like that and with difficulties.
The workers are facing great barriers whenever they try to organise. And as I was previously saying, the factory owners and government are super colluded.
To give you some sense of this, in 2016 and 2019, the workers faced two massive crackdowns, where thousands of them lost their jobs.
They were blacklisted and their voices were criminalised. A few dozen criminal charges were brought against some workers. It was just because they were calling for an increase to minimum wages.
So, they’re criminalised for asking for better wages?
Right. And these two areas haven’t improved. But, safety has improved. And the workers are much more knowledgeable than before about their rights.
In my time, the worker would not know where they needed to go when they faced a problem. But, today, they may not know about all of their rights, but they know that there are some organisations where they can go and ask for help, whenever they face problems.
Looking back to Australia, does BCWS know of any brands or companies that it can point the finger at for being involved in the distribution of products that might be made under exploitational conditions?
All of them. And if we talk about whether they are treating the workers better than any other western brands, no, they’re not.
All of their sourcing factories are paying low wages to workers. They’re not paying living wages. The workers are not free to exercise their rights. They are facing gender-based violence in those factories.
And as for Just Jeans, they didn’t sign the Accord, so their workers are working in unsafe buildings.
Many western nations have been enacting modern slavery laws that require that businesses to check for any evidence of exploitational practices. Are these laws having an effect on the garment factory practices in your country?
Not yet. But, there is one law that France has, which is the due diligence law. It makes a brand responsible for their whole supply line. If that kind of law was adopted by the Australian government that would help.
But, at this moment, modern slavery laws are not helping. Modern slavery has a lot of definitions. If you talk to the manufacturers here, they will say there is no modern slavery.
But, putting workers on long shifts and low wages that is modern slavery. But, they have their own definitions.
And lastly, Ms Akter, if you were standing next to someone in Sydney who was contemplating purchasing a cheap item of clothing that was likely made under the conditions you’ve described, what would you say to them?
Still buy the clothes that were made in Bangladesh, or any other producing country, because we need these jobs. But, we want these jobs with dignity. And as a consumer, you can do a lot of things to get that dignity.
For us, a dignified job is when we have rights, or we are free to exercise rights. We have a living wage. Our factories are gender-based violence free. And we are working in a safe workplace.
That’s a dignified job. And how a consumer can help bring this about is by raising their voice. Buy the clothes, but at the same time, ask more questions of the brands. Tell them you want to know about the human faces who made the clothes.
They can ask the brands directly. And that can start at the store. They can do letter campaigns. They could do phone campaigns. And trust me, that will ring bells in the bosses’ room, because the store managers will be reporting to their bosses.
For a consumer, I would say, don’t rush to a price tag, think about the human face behind it.